Kuyu Altı Kimyasal Enjeksiyon Hatları-Neden Arızalanır?Deneyimler, Zorluklar ve Yeni Test Yöntemlerinin Uygulanması
Copyright 2012, Petrol Mühendisleri Derneği
Soyut
Statoil, kuyu içi sürekli kireç önleyici enjeksiyonunun uygulandığı çeşitli alanlarda faaliyet göstermektedir.Amaç, üst boruyu ve emniyet valfini (Ba/Sr) SO4 veya CaCO'dan korumaktır;Ölçek sıkıştırmanın düzenli olarak gerçekleştirilmesinin zor ve maliyetli olabileceği durumlarda, örneğin deniz altı alanlarının bağlanması.
Sürekli kireç önleyici aşağı kuyu enjeksiyonu, üretim paketleyicinin üzerinde kireçlenme potansiyeli olan kuyularda üst boruları ve emniyet valfini korumak için teknik olarak uygun bir çözümdür;özellikle yakın kuyu alanındaki kireçlenme potansiyeli nedeniyle düzenli olarak sıkılması gerekmeyen kuyularda.
Kimyasal enjeksiyon hatlarının tasarlanması, işletilmesi ve bakımı, malzeme seçimine, kimyasal kalifikasyona ve izlemeye ekstra odaklanma gerektirir.Sistemin basıncı, sıcaklığı, akış rejimleri ve geometrisi, güvenli çalışmayı zorlaştırabilir.Üretim tesisinden deniz altı şablonuna kadar birkaç kilometre uzunluğundaki enjeksiyon hatlarında ve kuyulardaki enjeksiyon valflerinde zorluklar tespit edilmiştir.
Delik içi sürekli enjeksiyon sistemlerinin çökelme ve korozyon sorunları ile ilgili karmaşıklığını gösteren saha deneyimleri tartışılmaktadır.Laboratuvar çalışmaları ve kimyasal kalifikasyon için yeni yöntemlerin uygulanması temsil edilmektedir.Multidisipliner eylemlere yönelik ihtiyaçlar ele alınmaktadır.
giriiş
Statoil, kuyu içi sürekli kimyasal enjeksiyonunun uygulandığı çeşitli alanlarda faaliyet göstermektedir.Bu esas olarak, amacın üst boruyu ve kuyu içi emniyet valfini (DHSV) (Ba/Sr) SO4 veya CaCO'dan korumak olduğu kireç önleyici (SI) enjeksiyonunu içerir;ölçek.Bazı durumlarda emülsiyon kırıcı, ayırma sürecini kuyunun mümkün olduğu kadar derinine ve nispeten yüksek bir sıcaklıkta başlatmak için kuyuya enjekte edilir.
Kuyuların üretim paketleyicisinin yukarısında kireçlenme potansiyeli olan üst kısımlarını korumak için kuyuya sürekli kireç önleyici enjeksiyonu teknik olarak uygun bir çözümdür.Sürekli enjeksiyon, özellikle yakın kuyularda düşük kabuklanma potansiyeli nedeniyle sıkılması gerekmeyen kuyularda önerilebilir;veya düzenli olarak yapılmasının zor ve maliyetli olabileceği durumlarda, örneğin deniz altı alanlarının bağlanması.
Statoil, sürekli kimyasal enjeksiyon konusundaki deneyimini üst taraf sistemlerine ve deniz altı şablonlarına genişletmiştir, ancak yeni zorluk, enjeksiyon noktasını kuyunun daha derinlerine taşımaktır.Kimyasal enjeksiyon hatlarının tasarlanması, işletilmesi ve bakımı çeşitli konulara ekstra odaklanma gerektirir;malzeme seçimi, kimyasal yeterlilik ve izleme gibi.Sistemin basıncı, sıcaklığı, akış rejimleri ve geometrisi, güvenli çalışmayı zorlaştırabilir.Üretim tesisinden deniz altı şablonuna ve kuyulardaki enjeksiyon vanalarına kadar uzanan uzun (birkaç kilometre) enjeksiyon hatlarındaki zorluklar belirlenmiştir;Şekil 1.Enjeksiyon sistemlerinin bir kısmı planlandığı gibi çalışırken, bir kısmı da çeşitli sebeplerden dolayı arızalanmıştır.Kuyu içi kimyasal enjeksiyon (DHCI) için birkaç yeni saha geliştirmesi planlanmaktadır;Yine de;bazı durumlarda ekipman henüz tam olarak kalifiye edilmemiştir.
DHCI uygulaması karmaşık bir iştir.Tamamlanma ve kuyu tasarımlarını, kuyu kimyasını, borda sistemini ve borda prosesinin kimyasal dozaj sistemini içerir.Kimyasal, üst taraftan kimyasal enjeksiyon hattı yoluyla tamamlama ekipmanına ve kuyuya pompalanacaktır.Bu nedenle, bu tür projelerin planlanması ve yürütülmesinde çeşitli disiplinler arasındaki işbirliği çok önemlidir.Çeşitli hususların değerlendirilmesi gerekir ve tasarım sırasında iyi iletişim önemlidir.Kuyu kimyası, malzeme seçimi, akış güvencesi ve üretim kimyasal yönetimi konularıyla ilgilenen proses mühendisleri, denizaltı mühendisleri ve tamamlama mühendisleri yer alır.Zorluklar, kimyasal tabanca kralı veya sıcaklık kararlılığı, korozyon ve bazı durumlarda kimyasal enjeksiyon hattındaki yerel basınç ve akış etkilerinden kaynaklanan vakum etkisi olabilir.Bunlara ek olarak yüksek basınç, yüksek sıcaklık, yüksek gaz oranı, yüksek kireçlenme potansiyeli gibi durumlar,kuyudaki uzun mesafe göbek ve derin enjeksiyon noktası, enjekte edilen kimyasala ve enjeksiyon valfine farklı teknik zorluklar ve gereksinimler verir.
Statoil operasyonlarında kurulan DHCI sistemlerine genel bir bakış, deneyimin her zaman başarılı olmadığını göstermektedir Tablo 1. Ancak, enjeksiyon tasarımının, kimyasal kalifikasyonun, işletimin ve bakımın iyileştirilmesi için planlama yapılmaktadır.Zorluklar sahadan sahaya değişir ve problem mutlaka kimyasal enjeksiyon valfinin kendisinin çalışmaması değildir.
Son yıllarda kuyu içi kimyasal enjeksiyon hatlarıyla ilgili çeşitli zorluklar yaşandı.Bu yazıda bu deneyimlerden bazı örnekler verilmiştir.Makale, DHCI hatlarıyla ilgili sorunları çözmek için alınan önlemleri ve alınan önlemleri tartışıyor.İki vaka geçmişi verilmiştir;biri korozyon ve diğeri kimyasal silah kralı hakkında.Delik içi sürekli enjeksiyon sistemlerinin çökelme ve korozyon sorunları ile ilgili karmaşıklığını gösteren saha deneyimleri tartışılmaktadır.
Laboratuvar çalışmaları ve kimyasal kalifikasyon için yeni yöntemlerin uygulanması da dikkate alınır;kimyasalın nasıl pompalanacağı, kireçlenme potansiyeli ve önleme, karmaşık ekipman uygulaması ve kimyasalın geri üretildiğinde borda sistemini nasıl etkileyeceği.Kimyasal uygulama için kabul kriterleri; çevre sorunları, verimlilik, üst taraftaki depolama kapasitesi, pompa hızı, mevcut pompanın kullanılıp kullanılamayacağı vb. ve bu hatların çevresindeki malzemeler.Enjeksiyon hattının gaz istilasından dolayı tıkanmasını önlemek için kimyasalın hidrat ile engellenmesi gerekebilir ve kimyasalın nakliye ve depolama sırasında donmaması gerekir.Mevcut dahili yönergelerde, sistemin her noktasına hangi kimyasalların uygulanabileceğine dair bir kontrol listesi bulunmaktadır. Viskozite gibi fiziksel özellikler önemlidir.Enjeksiyon sistemi, göbekten 3-50km mesafeli deniz altı akış hattını ve kuyunun 1-3km aşağısını ifade edebilir.Bu nedenle, sıcaklık kararlılığı da önemlidir.Aşağı akış etkilerinin değerlendirilmesi, örneğin rafinerilerde de dikkate alınması gerekebilir.
Kuyu içi kimyasal enjeksiyon sistemleri
Fayda maliyet
DHS V veya üretim tüpünü korumak için kuyuya sürekli kireç önleyici enjeksiyonu, kuyuyu kireç önleyici ile sıkıştırmaya kıyasla daha uygun maliyetli olabilir.Bu uygulama, tufal sıkıştırma işlemlerine kıyasla oluşum hasarı potansiyelini azaltır, tufal sıkışmalarından sonra potansiyel proses problemlerini azaltır ve kimyasal enjeksiyon hızını üstten enjeksiyon sisteminden kontrol etme imkanı verir.Enjeksiyon sistemi aynı zamanda diğer kimyasalları sürekli olarak aşağı kuyuya enjekte etmek için de kullanılabilir ve böylece proses tesisinin aşağısında meydana gelebilecek diğer zorlukları azaltabilir.
Oseberg S veya sahasının kuyu içi ölçekli bir stratejisini geliştiren kapsamlı bir çalışma yapılmıştır.En büyük ölçekli endişe CaCO idi;üst boruda kireçlenme ve olası DHSV arızası.Oseberg S veya ölçek yönetimi stratejisi değerlendirmeleri, üç yıllık bir süre boyunca DHCI'nin kimyasal enjeksiyon hatlarının çalıştığı kuyularda en uygun maliyetli çözüm olduğu sonucuna vardı.Rekabet eden tufal sıkıştırma tekniği ile ilgili olarak ana maliyet unsuru, kimyasal/operasyonel maliyetten ziyade ertelenmiş yağdı.Gaz kaldırmada tufal önleyicinin uygulanması için, kimyasal maliyet üzerindeki ana faktör, yüksek SI konsantrasyonuna yol açan yüksek gaz kaldırma oranıydı, çünkü kimyasal tabanca kralından kaçınmak için konsantrasyonun gaz kaldırma hızıyla dengelenmesi gerekiyordu.Oseberg S'deki veya iyi işleyen DHC I hatlarına sahip iki kuyu için bu seçenek, DHS V'leri CaCO'ya karşı korumak için seçildi;ölçeklendirme
Sürekli enjeksiyon sistemi ve valfler
Sürekli kimyasal enjeksiyon sistemlerini kullanan mevcut tamamlama çözümleri, kılcal hatların tıkanmasını önleme konusunda zorluklarla karşılaşmaktadır.Tipik olarak enjeksiyon sistemi, bir yüzey manifolduna bağlanan, içinden beslenen ve borunun halka şeklindeki tarafındaki boru askısına bağlanan 1/4” veya 3/8” dış çaplı (OD) bir kılcal hattan oluşur.Kılcal hat, özel boru bileziği kelepçeleri ile üretim borusunun dış çapına bağlanır ve borunun dışında kimyasal enjeksiyon mandreline kadar uzanır.Mandrel, enjekte edilen kimyasala yeterli dağılma süresi vermek ve kimyasalı zorlukların bulunduğu yere yerleştirmek amacıyla geleneksel olarak DHS V'nin yukarı akışına veya kuyunun daha derinine yerleştirilir.
Kimyasal enjeksiyon valfinde, Şekil 2, çapı yaklaşık 1,5 inç olan küçük bir kartuş, kuyu deliği sıvılarının kılcal hatta girmesini önleyen çek valfleri içerir.Bu sadece bir yaya binen küçük bir poppet.Yay kuvveti, popeti sızdırmazlık yuvasından açmak için gereken basıncı belirler ve tahmin eder.Kimyasal akmaya başladığında, popet yuvasından kaldırılır ve çek valfi açar.
İki adet çek valf takılması zorunludur.Bir valf, kuyu deliği sıvılarının kılcal hatta girmesini önleyen birincil bariyerdir.Bu, nispeten düşük bir açılış basıncına (2-15 bar) sahiptir. Kılcal boru hattı içindeki hidrostatik basınç, kuyu deliği basıncından düşükse, kuyu sıvıları kılcal boru hattına girmeye çalışacaktır.Diğer çek valf, 130-250 bar atipik açılma basıncına sahiptir ve U-tüpü önleme sistemi olarak bilinir.Bu valf, kılcal hattın içindeki hidrostatik basıncın, üretim borusunun içindeki kimyasal enjeksiyon noktasındaki kuyu deliği basıncından daha yüksek olması durumunda, kılcal hattın içindeki kimyasalın kuyu deliğine serbestçe akmasını önler.
İki çek valfe ek olarak, normalde bir sıralı filtre vardır ve bunun amacı, çek valf sistemlerinin sızdırmazlık özelliklerini herhangi bir türde pisliğin tehlikeye atmamasını sağlamaktır.
Açıklanan çek valflerin boyutları oldukça küçüktür ve enjekte edilen sıvının temizliği, işlevsel işlevsellikleri için çok önemlidir.Kapiler hattın içindeki akış hızının artırılmasıyla sistemdeki birikintilerin temizlenebileceğine ve böylece çek valflerin isteyerek açılabileceğine inanılmaktadır.
Çekvalf açıldığında, akan basınç hızla düşer ve basınç tekrar yükselene kadar kılcal hatta yukarı doğru ilerler.Çek valf daha sonra, kimyasalların akışı valfi açmak için yeterli basıncı oluşturana kadar kapanacaktır;sonuç, çek valf sistemindeki basınç salınımlarıdır.Çek valf sisteminin açma basıncı ne kadar yüksek olursa, çek valf açıldığında o kadar az akış alanı oluşur ve sistem denge koşullarını sağlamaya çalışır.
Kimyasal enjeksiyon valfleri nispeten düşük bir açma basıncına sahiptir;ve kimyasal giriş noktasındaki boru basıncı, kılcal boru hattı içindeki kimyasalların hidrostatik basıncı ile çek valf açma basıncının toplamından az olursa, vakuma yakın veya kılcal hattın üst kısmında vakum oluşacaktır.Kimyasal enjeksiyonu durduğunda veya kimyasal akışı düşük olduğunda, kılcal hattın üst kısmında vakuma yakın koşullar oluşmaya başlayacaktır.
Vakum seviyesi, kuyu deliği basıncına, kapiler hat içinde kullanılan enjekte edilen kimyasal karışımın özgül ağırlığına, enjeksiyon noktasındaki çekvalf açma basıncına ve kılcal hat içindeki kimyasalın akış hızına bağlıdır.Kuyu koşulları saha ömrü boyunca değişiklik gösterecek ve bu nedenle vakum potansiyeli de zaman içinde değişecektir.Beklenen zorluklar ortaya çıkmadan önce doğru değerlendirmeyi ve önlemi almak için bu durumun farkında olmak önemlidir.
Düşük enjeksiyon hızlarıyla birlikte, tipik olarak bu tür uygulamalarda kullanılan solventler buharlaşarak tam olarak keşfedilmemiş etkilere neden olur.Bu etkiler, çözücü buharlaşırken polimerler gibi katıların çökelmesi veya silah kralıdır.
Ayrıca, galvanik hücreler, kimyasalın sıvı yüzeyi ile yukarıdaki vakuma yakın gaz fazı arasındaki geçiş fazında oluşturulabilir.Bu, bu koşullar altında kimyasalın artan agresifliğinin bir sonucu olarak kılcal hat içinde yerel oyuklaşma korozyonuna yol açabilir.Kapiler hattın içi kurudukça içinde bir film halinde oluşan pullar veya tuz kristalleri, kılcal hattı sıkıştırabilir veya tıkayabilir.
Kuyu bariyeri felsefesi
Sağlam kuyu çözümleri tasarlarken Statoil, kuyunun kullanım ömrü boyunca her zaman kuyu güvenliğinin yerinde olmasını şart koşar.Bu nedenle Statoil, sağlam iki bağımsız kuyu bariyeri olmasını gerektirir.Şekil 3, atipik kuyu bariyeri şemasını göstermektedir; burada mavi renk, birincil kuyu bariyeri zarfını temsil etmektedir;bu durumda üretim hortumu.Kırmızı renk, ikincil bariyer zarfını temsil eder;kasa.Çizimin sol tarafında kimyasal enjeksiyon, kırmızı işaretli alanda (ikincil bariyer) üretim borusuna enjeksiyon noktası olan siyah bir çizgi olarak gösterilir.Kuyuya kimyasal enjeksiyon sistemleri sokarak, hem birincil hem de ikincil kuyu deliği bariyerleri tehlikeye atılır.
Korozyon vaka geçmişi
olayların sırası
Statoil tarafından Norveç Kıta Sahanlığı'nda işletilen bir petrol sahasına kuyu içi kireç önleyici kimyasal enjeksiyonu uygulandı.Bu durumda, uygulanan tufal önleyici orijinal olarak karada ve deniz altı uygulamaları için uygun bulunmuştur.Kuyunun yeniden tamamlanmasını, DHCIpointat2446mMD, Şekil 3'ün kurulumu izledi.Üst taraf kireç önleyicinin kuyuya enjeksiyonu, kimyasalın başka bir testi yapılmadan başlatıldı.
Bir yıllık işletme sonunda kimyasal enjeksiyon sisteminde kaçaklar gözlemlendi ve incelemelere başlandı.Sızıntı, kuyu bariyerleri üzerinde zararlı bir etkiye sahipti.Birkaç kuyuda benzer olaylar meydana geldi ve soruşturma devam ederken bazılarının kapatılması gerekti.
Üretim hortumu çekildi ve ayrıntılı olarak incelendi.Aşınma saldırısı borunun bir tarafıyla sınırlıydı ve bazı boru bağlantıları o kadar aşınmıştı ki içlerinde delikler vardı.Yaklaşık 8,5 mm kalınlığında %3 krom çeliği 8 aydan daha kısa bir sürede parçalandı.Ana korozyon, kuyu başından yaklaşık 380 m MD'ye kadar kuyunun üst kısmında meydana geldi ve en kötü korozyona uğramış boru bağlantıları yaklaşık 350 m MD'de bulundu.Bu derinliğin altında çok az korozyon gözlendi veya hiç gözlenmedi, ancak boru dış çaplarında çok fazla kalıntı bulundu.
9-5/8'' kasa da kesilip çekildi ve benzer etkiler gözlemlendi;sadece bir tarafta kuyunun üst kısmında korozyon ile.Sızıntıya kasanın zayıflamış bölümünün patlaması neden oldu.
Kimyasal enjeksiyon hattı malzemesi Alaşım 825 idi.
Kimyasal yeterlilik
Kimyasal özellikler ve korozyon testi, tufal önleyicilerin nitelendirilmesinde önemli odak noktalarıdır ve gerçek tufal önleyici, birkaç yıldır karada ve deniz altı uygulamalarında kalifiye edilmiş ve kullanılmıştır.Asıl kimyasal kuyu altının uygulanmasının nedeni, mevcut kuyu altı kimyasalının değiştirilmesiyle çevresel özelliklerin iyileştirilmesiydi. Bununla birlikte, tortu önleyici yalnızca ortam üst tarafı ve deniz tabanı sıcaklıklarında (4-20°C) kullanılmıştı.Kuyuya enjekte edildiğinde, kimyasalın sıcaklığı 90°C'ye kadar çıkabilir, ancak bu sıcaklıkta daha fazla test yapılmamıştır.
Kimyasal tedarikçisi tarafından ilk aşındırıcılık testleri yapılmış ve sonuçlar karbon çeliği için yüksek sıcaklıkta 2-4 mm/yıl göstermiştir.Bu aşamada, operatörün malzeme teknik yeterliliği minimum düzeyde tutulmuştur.Operatör tarafından daha sonra yeni testler yapıldı ve tufal önleyicinin üretim borusundaki ve üretim kasasındaki malzemeler için 70 mm/yıl'ı aşan korozyon oranlarıyla oldukça aşındırıcı olduğunu gösterdi.Kimyasal enjeksiyon hattı malzemesi Alaşım 825, enjeksiyondan önce kireç önleyiciye karşı test edilmemiştir.Kuyu sıcaklığı 90°C'ye ulaşabilir ve bu koşullar altında yeterli testler yapılmış olmalıdır.
Araştırma ayrıca, konsantre çözelti olarak kireç önleyicinin <3.0 pH bildirdiğini ortaya çıkardı.Bununla birlikte, pH ölçülmemiştir.Daha sonra ölçülen pH, pH 0-1 gibi çok düşük bir değer gösterdi.Bu, verilen pH değerlerine ek olarak ölçümlere ve malzeme hususlarına olan ihtiyacı göstermektedir.
Sonuçların yorumlanması
Enjeksiyon hattı (Şekil 3), enjeksiyon noktasında kuyudaki basıncı aşan kireç önleyicinin hidrostatik basıncını verecek şekilde yapılmıştır.İnhibitör, kuyu deliğinde var olandan daha yüksek bir basınçta enjekte edilir.Bu, kuyunun kapanmasında bir U-tüpü etkisi ile sonuçlanır.Valf, enjeksiyon hattında her zaman kuyudakinden daha yüksek bir basınçla açılacaktır.Bu nedenle enjeksiyon hattında vakum veya buharlaşma meydana gelebilir.Korozyon hızı ve çukurlaşma riski, solventin buharlaşmasından dolayı gaz/sıvı geçiş bölgesinde en fazladır.Kuponlar üzerinde yapılan laboratuvar deneyleri bu teoriyi doğruladı.Sızıntının yaşandığı kuyularda enjeksiyon hatlarındaki tüm delikler kimyasal enjeksiyon hattının üst kısmında yer alıyordu.
Şekil 4, belirgin oyuk korozyonu olan DHC I hattının fotoğrafını göstermektedir.Dış üretim borusunda görülen korozyon, çukurlaşma sızıntı noktasından yerel olarak kireç önleyicinin açığa çıktığını gösterdi.Sızıntıya, yüksek derecede aşındırıcı kimyasalın neden olduğu oyuk korozyonu ve kimyasal enjeksiyon hattından üretim muhafazasına sızıntı neden olmuştur.Kireç önleyici, çukurlu kılcal hattan kasaya ve boruya püskürtüldü ve sızıntılar meydana geldi.Enjeksiyon hattındaki sızıntıların ikincil sonuçları dikkate alınmamıştır.Muhafaza ve boru korozyonunun, çukurlu kılcal hattan muhafaza ve boruya yayılan konsantre kireç önleyicilerin bir sonucu olduğu sonucuna varıldı, Şekil 5.
Bu davada, malzeme yeterlilik mühendislerinin katılımı eksikti.DHCI hattındaki kimyasalın aşındırıcılığı test edilmemiştir ve sızıntıdan kaynaklanan ikincil etkiler değerlendirilmemiştir;çevredeki malzemelerin kimyasal maruziyeti tolere edip edemeyeceği gibi.
Kimyasal silah kralının vaka geçmişi
olayların sırası
Bir HP HT alanı için kireç önleme stratejisi, kuyu içi emniyet valfinin akış yukarısında sürekli kireç önleyici enjeksiyonuydu.Kuyuda ciddi bir kalsiyum karbonat tortulaşma potansiyeli tespit edildi.Zorluklardan biri, düşük su üretim oranıyla birlikte yüksek sıcaklık ve yüksek gaz ve kondensat üretim oranlarıydı.Kireç inhibitörünün enjekte edilmesiyle ilgili endişe, çözücünün yüksek gaz üretim hızı tarafından sıyrılması ve kimyasalın silah kralının kuyudaki emniyet valfinin akış yukarısındaki enjeksiyon noktasında oluşmasıydı, Şekil 1.
Kireç önleyicinin kalifikasyonu sırasında, üst kısım proses sistemindeki (düşük sıcaklık) davranış da dahil olmak üzere, ürünün HP HT koşullarındaki etkinliğine odaklanılmıştır.Yüksek gaz oranı nedeniyle üretim hortumunda tufal inhibitörünün kendisinin çökelmesi ana sorundu.Laboratuvar testleri, tortu önleyicinin çökebileceğini ve boru duvarına yapışabileceğini gösterdi.Bu nedenle emniyet valfinin çalıştırılması riski ortadan kaldırabilir.
Deneyimler, birkaç haftalık çalışmadan sonra kimyasal hattın sızdırdığını gösterdi.Kılcal hatta kurulan yüzey göstergesinde kuyu deliği basıncını izlemek mümkündü.İyi bir bütünlük elde etmek için hat izole edildi.
Kimyasal enjeksiyon hattı kuyudan çekildi, açıldı ve sorunun tespiti ve olası arıza sebeplerinin bulunması için kontrol edildi.Şekil 6'da görülebileceği gibi, önemli miktarda çökelti bulundu ve kimyasal analiz, bunun bir kısmının tufal önleyici olduğunu gösterdi.Çökelti contada bulunuyordu ve popet ve valf çalıştırılamadı.
Valf arızasına, valf sisteminin içindeki birikintilerin, çek valflerin metalden metale yuvayı yemesini engellemesi neden oldu.Döküntü incelendi ve ana parçacıkların, muhtemelen kılcal boru hattının döşenmesi sırasında üretilen metal talaşları olduğu kanıtlandı.Ek olarak, her iki çek valfte, özellikle valflerin arka tarafında bazı beyaz birikintiler tespit edildi.Bu, alçak basınç tarafıdır, yani taraf her zaman kuyu deliği sıvıları ile temas halinde olacaktır.Başlangıçta, valfler sıkışarak açıldığından ve kuyu deliği sıvılarına maruz kaldığından, bunun üretim kuyu deliğinden gelen döküntü olduğuna inanılıyordu.Ancak inceleme, kalıntının kireç önleyici olarak kullanılan kimyasalla benzer kimyaya sahip polimerler olduğunu kanıtladı.Bu ilgimizi çekti ve Statoil kılcal hatta bulunan bu polimer kalıntılarının arkasındaki nedenleri araştırmak istedi.
Kimyasal yeterlilik
Bir HP HT alanında, çeşitli üretim problemlerini hafifletmek için uygun kimyasalların seçimine ilişkin birçok zorluk vardır.Kuyu içi sürekli enjeksiyon için tufal inhibitörünün kalifikasyonunda, aşağıdaki testler gerçekleştirilmiştir:
● Ürün kararlılığı
● Termal yaşlanma
● Dinamik performans testleri
● Formasyon suyu ve hidrat inhibitörü (MEG) ile uyumluluk
● Statik ve dinamik top kralı testi
● Yeniden çözünme bilgisi su, taze kimyasal ve MEG
Kimyasal önceden belirlenmiş bir dozaj oranında enjekte edilecektir.,ancak su üretimi mutlaka sabit olmayacaktır.,yani su akması.Su salyangozları arasında,kimyasal kuyu deliğine girdiğinde,sıcak bir şekilde karşılanacak,hızlı akan hidrokarbon gazı akışı.Bu, bir gaz kaldırma uygulamasında kireç önleyici enjekte etmeye benzer (Fleming etal.2003).
yüksek gaz sıcaklığı,solvent sıyırma riski son derece yüksektir ve tabanca kralı enjeksiyon valfinin tıkanmasına neden olabilir.Bu, yüksek kaynama noktalı/düşük buhar basınçlı çözücüler ve diğer Buhar Basıncı Düşürücüler (VPD'ler) ile formüle edilmiş kimyasallar için bile bir risktir. Kısmi tıkanma durumunda,formasyon suyu akışı,MEG ve/veya taze kimyasal, suyu alınmış veya dışarı atılmış kimyasalı çıkarabilmeli veya yeniden çözebilmelidir.
Bu durumda, üretim sistemi olarak bir HP/HTg'deki enjeksiyon portlarının yakınındaki akış koşullarını kopyalamak için yeni bir laboratuvar test teçhizatı tasarlandı.Dinamik tabanca kral testlerinden elde edilen sonuçlar, önerilen uygulama koşulları altında önemli bir solvent kaybının kaydedildiğini göstermektedir.Bu, hızlı top kralına ve sonunda akış hatlarının bloke edilmesine yol açabilir.Bu nedenle çalışma, su üretiminden önce bu kuyularda sürekli kimyasal enjeksiyon için nispeten önemli bir risk olduğunu gösterdi ve bu alan için normal başlatma prosedürlerini ayarlama kararına yol açarak, su sızıntısı tespit edilene kadar kimyasal enjeksiyonu geciktirdi.
Sürekli enjeksiyon deliği için kireç önleyicinin niteliği, enjeksiyon noktasında ve akış hattında solvent sıyırma ve kireç önleyicinin tabanca kralına yüksek düzeyde odaklanmıştır, ancak enjeksiyon valfinin kendisinde tabanca kralı potansiyeli değerlendirilmemiştir.Önemli solvent kaybı ve hızlı tabanca kralı nedeniyle enjeksiyon valfi muhtemelen başarısız olmuştur.,Şekil 6. Sonuçlar, sistemin bütünsel bir görünümüne sahip olmanın önemli olduğunu göstermektedir.;sadece üretim zorluklarına odaklanmaz,aynı zamanda kimyasalın enjeksiyonu ile ilgili zorluklar,yani enjeksiyon valfi.
Diğer alanlardan deneyim
Uzun mesafeli kimyasal enjeksiyon hatlarıyla ilgili sorunlarla ilgili ilk raporlardan biri, Gull fak sandVig dis uydu alanlarındandı (Osa etal.2001). Üretilen sıvılardan gelen gazın istilası nedeniyle, deniz altı enjeksiyon hatlarının hat içinde hidrat oluşumu engellendi. enjeksiyon valfi aracılığıyla hatta.Deniz altı üretim kimyasallarının geliştirilmesi için yeni yönergeler geliştirilmiştir.Gereksinimler, deniz altı kalıplarına enjekte edilecek tüm su bazlı tufal önleyicilere partikül giderme (filtrasyon) ve hidrat inhibitörünün (örn. glikol) eklenmesini içeriyordu.Kimyasal stabilite,viskozite ve uyumluluk (sıvı ve malzemeler) de dikkate alınmıştır.Bu gereksinimler, Statoil sistemine daha da alınmıştır ve kuyu içi kimyasal enjeksiyonu içerir.
Oseberg S veya sahasının geliştirme aşamasında, tüm kuyuların DHC I sistemleriyle tamamlanması gerektiğine karar verildi(Fleming ve ark.2006). Amaç, CaCO'yu önlemekti.;SI enjeksiyonu ile üst boruda ölçeklendirme.Kimyasal enjeksiyon hatlarıyla ilgili en büyük zorluklardan biri, yüzey ile kuyu içi çıkış arasındaki iletişimi sağlamaktı.Kimyasal enjeksiyon hattının iç çapı, alan sınırlamaları nedeniyle halka emniyet valfi etrafında 7 mm'den 0,7 mm'ye (ID) daraldı ve sıvının bu bölümden taşınabilmesi başarı oranını etkiledi.Birkaç platform kuyusunda tıkalı kimyasal enjeksiyon hatları vardı,ancak nedeni anlaşılamadı.Çeşitli sıvıların katarları (glikol,ham,yoğunlaşma,ksilen,Ölçekli inhibitör,su vb.) viskozite ve uyumluluk açısından laboratuvarda test edilmiş ve hatları açmak için ileri ve geri akışta pompalanmıştır.;Yine de,hedef ölçek inhibitörü, kimyasal enjeksiyon valfine kadar tamamen pompalanamadı.Daha öte,bir kuyuda fosfonat tufal inhibitörünün tortusal CaClz tamamlama tuzlu suyuyla birlikte çökelmesi ve yüksek gazyağı oranı ve düşük su kesintisi olan bir kuyuda tortul inhibitörün gun king'i ile komplikasyonlar görüldü(Fleming etal.2006)
Dersler öğrenildi
Test yöntemi geliştirme
DHC I sistemlerinin başarısızlığından çıkarılan ana dersler, işlevsellik ve kimyasal enjeksiyonla ilgili değil, kireç önleyicinin teknik etkinliğiyle ilgili olmuştur.Borda enjeksiyonu ve deniz altı enjeksiyonu fazla mesaide iyi çalıştı;Yine de,uygulama, kimyasal kalifikasyon yöntemlerinde karşılık gelen bir güncelleme olmaksızın kuyu içi kimyasal enjeksiyonu içerecek şekilde genişletildi.Statoil'in sunulan iki saha vakasından elde ettiği deneyime göre, kimyasal kalifikasyon için geçerli belgeler veya yönergeler bu tür kimyasal uygulamaları içerecek şekilde güncellenmelidir.Başlıca iki zorluk, i) kimyasal enjeksiyon hattındaki vakum ve ii) kimyasalın potansiyel çökelmesi olarak tanımlanmıştır.
Üretim borusunda (tabanca ana kasasında görüldüğü gibi) ve enjeksiyon hortumunda (vakum kutusunda geçici bir arayüz tanımlanmıştır) kimyasalın buharlaşması meydana gelebilir, bu çökeltilerin akışla birlikte hareket etmesi ve enjeksiyon valfine ve ayrıca kuyunun içine.Enjeksiyon valfi genellikle enjeksiyon noktasının akış yukarısında bir filtre ile tasarlanır.,bu bir meydan okuma,yağış durumunda olduğu gibi, bu filtre tıkanarak valfin arızalanmasına neden olabilir.
Öğrenilen derslerden elde edilen gözlemler ve ön sonuçlar, fenomen üzerine kapsamlı bir laboratuvar çalışmasıyla sonuçlandı.Genel amaç, gelecekte benzer sorunlardan kaçınmak için yeni yeterlilik yöntemleri geliştirmekti.Bu çalışmada, kimyasalları belirlenen zorluklara göre incelemek için çeşitli testler yapılmış ve çeşitli laboratuvar yöntemleri tasarlanmıştır (geliştirilmiştir).
● Kapalı sistemlerde filtre tıkanmaları ve ürün kararlılığı.
● Kısmi çözücü kaybının kimyasalların aşındırıcılığına etkisi.
● Bir kılcal boru içindeki kısmi solvent kaybının katıların veya viskoz tıkaçların oluşumu üzerindeki etkisi.
Laboratuvar yöntemlerinin testleri sırasında birkaç potansiyel sorun tespit edilmiştir.
● Tekrarlanan filtre tıkanmaları ve zayıf kararlılık.
● Bir kılcal borudan kısmi buharlaşmanın ardından katı oluşumu
● Solvent kaybı nedeniyle PH değişir.
Yürütülen testlerin doğası, belirli koşullara tabi tutulduğunda kılcal damarlardaki kimyasalların fiziksel özelliklerindeki değişikliklerle ilgili ek bilgi ve bilgiler de sağlamıştır.,ve bunun benzer koşullara tabi toplu çözümlerden nasıl farklı olduğu.Test çalışması, aynı zamanda, dökme sıvı arasındaki önemli farklılıkları da belirlemiştir.,artan çökelme potansiyeline ve/veya artan aşındırıcılığa yol açabilen buhar fazları ve artık sıvılar.
Ölçek inhibitörlerinin aşındırıcılığı için test prosedürü geliştirilmiş ve yönetim belgelerine dahil edilmiştir.Her bir uygulama için, tufal inhibitörü enjeksiyonunun uygulanabilmesi için genişletilmiş aşındırıcılık testinin gerçekleştirilmesi gerekiyordu.Enjeksiyon hattındaki kimyasalın gun king testleri de yapılmıştır.
Bir kimyasalın kalifikasyonuna başlamadan önce, kimyasalın zorluklarını ve amacını açıklayan bir çalışma kapsamı oluşturmak önemlidir.İlk aşamada, sorunu çözecek kimyasal(lar)ın türlerini seçebilmek için ana zorlukları belirlemek önemlidir.En önemli kabul kriterlerinin bir özeti Tablo 2'de bulunabilir.
Kimyasalların kalifikasyonu
Kimyasalların kalifikasyonu, her uygulama için hem testlerden hem de teorik değerlendirmelerden oluşur.Teknik özellikler ve test kriterleri tanımlanmalı ve oluşturulmalıdır.,örneğin HSE içinde,malzeme uyumluluğu,ürün stabilitesi ve ürün kalitesi (parçacıklar).Daha öte,donma noktası,viskozite ve diğer kimyasallarla uyumluluk,hidrat inhibitörü,formasyon suyu ve üretilen sıvı belirlenmelidir.Kimyasalların kalifikasyonu için kullanılabilecek test yöntemlerinin basitleştirilmiş bir listesi Tablo 2'de verilmiştir.
Teknik verimliliğe sürekli odaklanma ve izleme,dozaj oranları ve HSE gerçekleri önemlidir.Bir ürünün gereksinimleri, bir tarlayı veya proses tesisi ömrünü değiştirebilir;üretim hızlarının yanı sıra sıvı bileşimine göre değişir.Performans değerlendirmesi ile takip faaliyeti,Optimum arıtma programını sağlamak için yeni kimyasalların optimizasyonu ve/veya test edilmesi sık sık yapılmalıdır.
Yağ kalitesine bağlı olarak,açık deniz üretim tesisinde su üretimi ve teknik zorluklar,ihracat kalitesini elde etmek için üretim kimyasallarının kullanılması gerekli olabilir,düzenleme gereksinimleri,ve açık deniz kurulumunu güvenli bir şekilde işletmek.Tüm alanların farklı zorlukları vardır ve ihtiyaç duyulan üretim kimyasalları, tarladan sahaya ve fazla mesaiye göre değişir.
Bir kalifikasyon programında üretim kimyasallarının teknik etkinliğine odaklanmak önemlidir.,ancak kimyasalın özelliklerine odaklanmak da çok önemlidir.,kararlılık gibi,ürün kalitesi ve uyumluluğu.Bu ayardaki uyumluluk, sıvılarla uyumluluk anlamına gelir,malzemeler ve diğer üretim kimyasalları.Bu bir meydan okuma olabilir.Daha sonra kimyasalın yeni zorluklara katkıda bulunduğunu veya yarattığını keşfetmek için bir sorunu çözmek için bir kimyasal kullanmak istenmez.Belki de en büyük zorluk teknik zorluk değil, kimyasalın özellikleridir.
Özel gereksinimler
Tedarik edilen ürünlerin filtrasyonuna ilişkin özel gereksinimler, deniz altı sistemi ve kuyu içi sürekli enjeksiyon için uygulanmalıdır.Kimyasal enjeksiyon sistemindeki süzgeçler ve filtreler, üst taraf enjeksiyon sisteminden aşağı akış ekipmanının özelliklerine göre sağlanmalıdır.,pompalar ve enjeksiyon valfleri,kuyu içi enjeksiyon valflerine.Kimyasalların kuyu içi sürekli enjeksiyonunun uygulandığı durumlarda, kimyasal enjeksiyon sistemindeki spesifikasyon, en yüksek kritikliğe sahip spesifikasyona dayanmalıdır.Bu belki de enjeksiyon valfi deliğindeki filtredir.
Enjeksiyon zorlukları
Enjeksiyon sistemi, 3-50 km'lik deniz altı göbek akış hattını ve kuyunun 1-3 km aşağısını ifade edebilir.Viskozite ve kimyasalları pompalayabilme gibi fiziksel özellikler önemlidir.Deniz dibi sıcaklığındaki viskozite çok yüksekse, kimyasalı deniz altı göbeğindeki kimyasal enjeksiyon hattından ve deniz altı enjeksiyon noktasına veya kuyuya pompalamak zor olabilir.Viskozite, beklenen depolama veya çalışma sıcaklığında sistem özelliklerine göre olmalıdır.Bu her durumda değerlendirilmeli,ve sisteme bağımlı olacaktır.Tablo olarak kimyasal enjeksiyon hızı, kimyasal enjeksiyonda başarı için bir faktördür.Kimyasal enjeksiyon hattının tıkanma riskini en aza indirmek için,Bu sistemdeki kimyasallar hidrat inhibe edilmelidir (eğer hidrat potansiyeli varsa).Sistemde bulunan sıvılar (koruma sıvısı) ve hidrat inhibitörü ile uyumluluk gerçekleştirilmelidir.Kimyasalın gerçek sıcaklıklarda stabilite testleri (mümkün olan en düşük ortam sıcaklığı),ortam sıcaklığı,denizaltı sıcaklığı,enjeksiyon sıcaklığı) geçilmelidir.
Belirli bir sıklıkta kimyasal enjeksiyon hatlarını yıkamak için bir program da düşünülmelidir.Kimyasal enjeksiyon hattını düzenli olarak solvent ile yıkamak önleyici bir etki sağlayabilir.,olası birikintileri birikmeden önce temizlemek için glikol veya temizleme kimyasalı kullanın ve hattın tıkanmasına neden olabilir.Yıkama sıvısının seçilen kimyasal çözeltisi,enjeksiyon hattındaki kimyasal ile uyumludur.
Bazı durumlarda kimyasal enjeksiyon hattı, bir alan ömrü ve sıvı koşulları boyunca farklı zorluklara dayalı çeşitli kimyasal uygulamalar için kullanılır.Su geçişinden önceki ilk üretim aşamasındaki ana zorluklar, genellikle artan su üretimiyle ilgili olan geç yaşam süresindeki sorunlardan farklı olabilir.Asfalt ene inhibitörü gibi sulu olmayan solvent bazlı inhibitörden tufal inhibitörü gibi su bazlı kimyasala geçiş uyumluluk konusunda zorluklara neden olabilir.Bu nedenle, kimyasal enjeksiyon hattındaki kimyasalın değiştirilmesi planlandığında ara parçaların uyumluluğuna ve kalifikasyonuna ve kullanımlarına odaklanmak önemlidir.
Malzemeler
Malzeme uyumluluğu ile ilgili,tüm kimyasallar contalarla uyumlu olmalıdır,elastomerler,kimyasal enjeksiyon sisteminde ve üretim tesisinde kullanılan contalar ve inşaat malzemeleri.Kuyu içi sürekli enjeksiyon için kimyasalların (örn. asidik kireç önleyici) aşındırıcılığına ilişkin test prosedürü geliştirilmelidir.Her uygulama için, kimyasalların enjeksiyonu uygulanmadan önce genişletilmiş aşındırıcılık testi yapılmalıdır.
Tartışma
Sürekli aşağı kuyu kimyasal enjeksiyonunun avantajları ve dezavantajları değerlendirilmelidir.DHS V veya üretim tüpünü korumak için sürekli kireç önleyici enjeksiyonu, kuyuyu kireçten korumak için zarif bir yöntemdir.Bu yazıda bahsedildiği gibi, sürekli aşağı kuyu kimyasal enjeksiyonunun çeşitli zorlukları vardır.,ancak riski azaltmak için çözümle bağlantılı olguları anlamak önemlidir.
Riski azaltmanın bir yolu, test yöntemi geliştirmeye odaklanmaktır.Deniz üstü veya deniz altı kimyasal enjeksiyonuna kıyasla kuyunun aşağısında daha farklı ve daha şiddetli koşullar vardır.Kimyasalların aşağı kuyuya sürekli enjeksiyonu için kimyasalların kalifikasyon prosedürü, koşullardaki bu değişiklikleri dikkate almalıdır.Kimyasalların kalifikasyonu, kimyasalların temas edebileceği malzemeye göre yapılmalıdır.Uyumluluk kalifikasyonu ve bu sistemlerin altında çalışacağı çeşitli kuyu yaşam döngüsü koşullarını mümkün olduğunca taklit eden koşullarda test etme gereklilikleri güncellenmeli ve uygulanmalıdır.Test yöntemi geliştirme, daha gerçekçi ve temsili testler için daha da geliştirilmelidir.
Ek olarak,kimyasallar ve ekipman arasındaki etkileşim başarı için esastır.Enjeksiyon kimyasal valflerinin geliştirilmesi, kuyudaki enjeksiyon valfinin kimyasal özelliklerini ve konumunu dikkate almalıdır.Test ekipmanının bir parçası olarak gerçek enjeksiyon valflerinin dahil edilmesi ve kalifikasyon programının bir parçası olarak kireç önleyici ve valf tasarımının performans testinin gerçekleştirilmesi düşünülmelidir.Ölçek inhibitörlerini nitelendirmek için,daha önce ana odak noktası süreç zorlukları ve ölçek engelleme olmuştur.,ancak iyi ölçek inhibisyonu, kararlı ve sürekli enjeksiyona bağlıdır.Kararlı ve sürekli enjeksiyon olmadan kireçlenme potansiyeli artacaktır.Kireç önleyici enjeksiyon valfi tıkalıysa ve sıvı akışına kireç önleyici enjeksiyon yoksa,Kuyu ve emniyet valfleri kireçten korunmaz ve bu nedenle güvenli üretim tehlikeye girebilir.Niteliklendirme prosedürü, kalifiye tufal inhibitörünün proses zorluklarına ve verimliliğine ek olarak, tufal inhibitörünün enjeksiyonuyla ilgili güçlüklerle ilgilenmelidir.
Yeni yaklaşım birkaç disiplini içermektedir ve disiplinler arasındaki işbirliği ve ilgili sorumlulukların açıklığa kavuşturulması gerekmektedir.Bu uygulamada üst taraf proses sistemi,deniz altı şablonları ve kuyu tasarımı ve tamamlamaları söz konusudur.Kimyasal enjeksiyon sistemleri için sağlam çözümler geliştirmeye odaklanan çok disiplinli ağlar önemlidir ve belki de başarıya giden yoldur.Çeşitli disiplinler arasındaki iletişim kritiktir;özellikle uygulanan kimyasalların kontrolünü elinde bulunduran kimyagerler ile kuyuda kullanılan ekipmanların kontrolünü elinde bulunduran kuyu mühendisleri arasındaki yakın iletişim önemlidir.Farklı disiplinlerin zorluklarını anlamak ve birbirinden öğrenmek, tüm sürecin karmaşıklığını anlamak için esastır.
Çözüm
● DHS'yi korumak için sürekli kireç önleyici enjeksiyonu V veya üretim boruları, kuyuyu kireçten korumak için zarif bir yöntemdir
● Belirlenen zorlukları çözmek için,aşağıdaki öneriler:
● Özel bir DHCI kalifikasyon prosedürü gerçekleştirilmelidir.
● Kimyasal enjeksiyon valfleri için yeterlilik yöntemi
● Kimyasal işlevsellik için test ve kalifikasyon yöntemleri
● Yöntem geliştirme
● İlgili malzeme testi
● İlgili çeşitli disiplinler arasındaki iletişimin başarı için çok önemli olduğu çok disiplinli etkileşim.
teşekkürler
Yazar, bu çalışmanın yayınlanmasına izin verdiği için Statoil AS A'ya ve Şekil 2'deki görüntünün kullanımına izin verdiği için Baker Hughes ve Schlumberger'e teşekkür eder.
terminoloji
(Ba/Sr)SO4=baryum/stronsiyum sülfat
CaCO3=kalsiyum karbonat
DHCI=delik altı kimyasal enjeksiyon
DHSV=delik içi emniyet valfi
örneğin = örneğin
GOR=mazot oranı
HSE= sağlık güvenlik ortamı
HPHT=yüksek basınç yüksek sıcaklık
ID=iç çap
yani= yani
km=kilometre
mm=milimetre
MEG=mono etilen glikol
mMD=metre ölçülen derinlik
OD=dış çap
SI=ölçek önleyici
mTV D=metre toplam dikey derinlik
U-tüpü=U şekilli tüp
VPD=buhar basıncı düşürücü
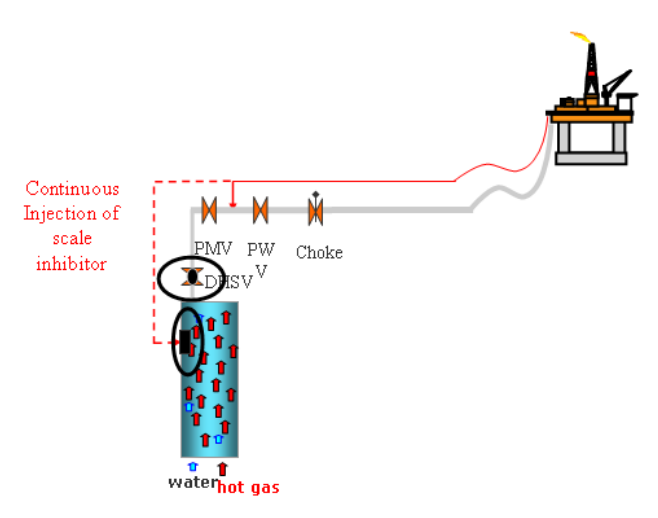
Şekil 1. Atipik alanda deniz altı ve kuyu içi kimyasal enjeksiyon sistemlerine genel bakış.DHSV akış yukarı kimyasal enjeksiyon taslağı ve ilgili beklenen zorluklar.DHS V=delik altı emniyet valfi, PWV=proses kanat valfi ve PM V=proses ana valfi.
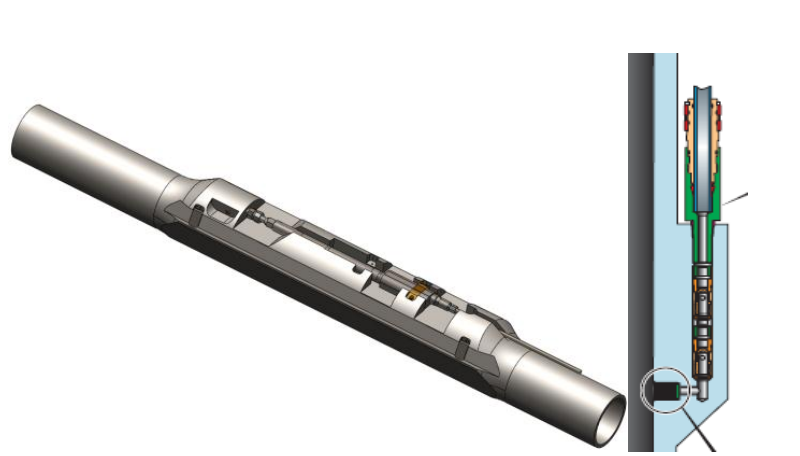
Şekil 2. Mandrel ve valf ile atipik kuyu içi kimyasal enjeksiyon sisteminin taslağı.Sistem, yüzey manifolduna bağlanır, içinden beslenir ve borunun halka şeklindeki tarafındaki boru askısına bağlanır.Kimyasal enjeksiyon mandreli geleneksel olarak kimyasal koruma sağlamak amacıyla kuyunun derinliklerine yerleştirilir.
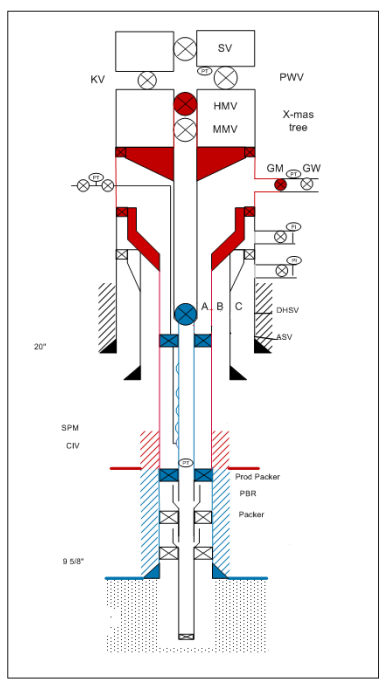
Şekil 3. Tipik kuyu bariyeri şeması,burada mavi renk birincil kuyu bariyer zarfını temsil eder;bu durumda üretim hortumu.Kırmızı renk, ikincil bariyer zarfını temsil eder;kasa.Sol tarafta, kırmızı işaretli alanda (ikincil bariyer) üretim borusuna enjeksiyon noktası olan kimyasal enjeksiyon, siyah çizgi gösterilir.
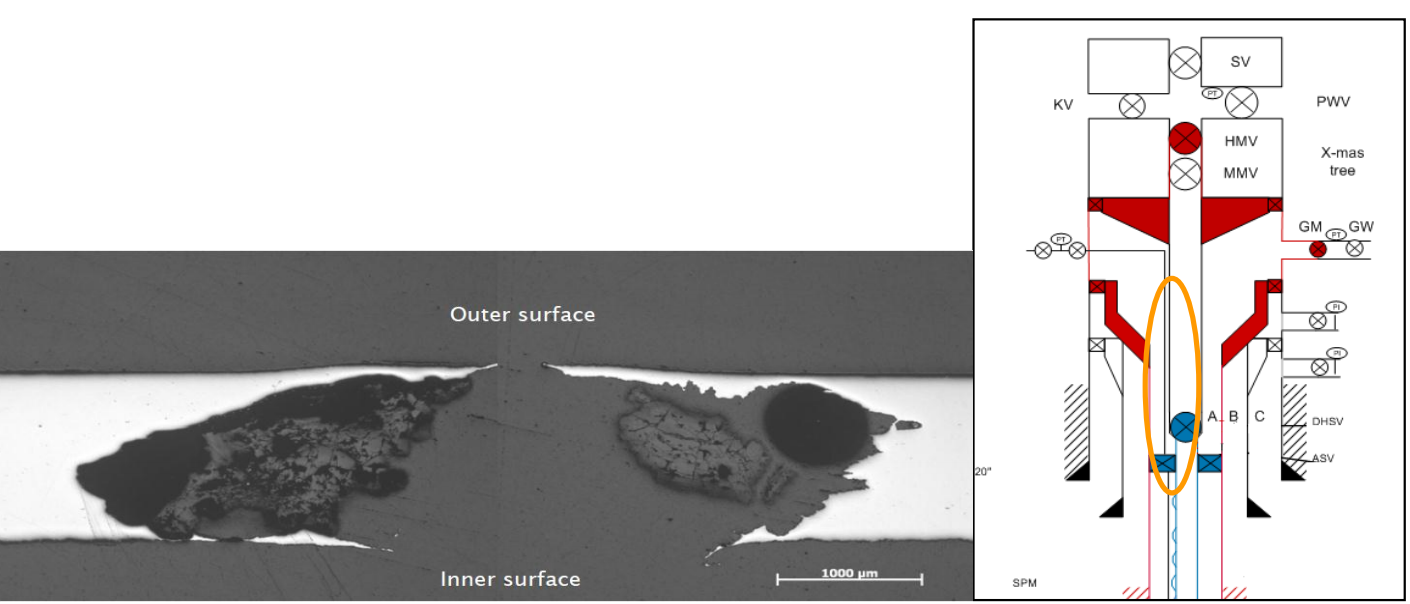
Şekil 4. 3/8” enjeksiyon hattının üst kısmında bulunan çukurlu delik.Alan, turuncu elips ile işaretlenmiş atipik kuyu bariyeri şemasında gösterilmektedir.
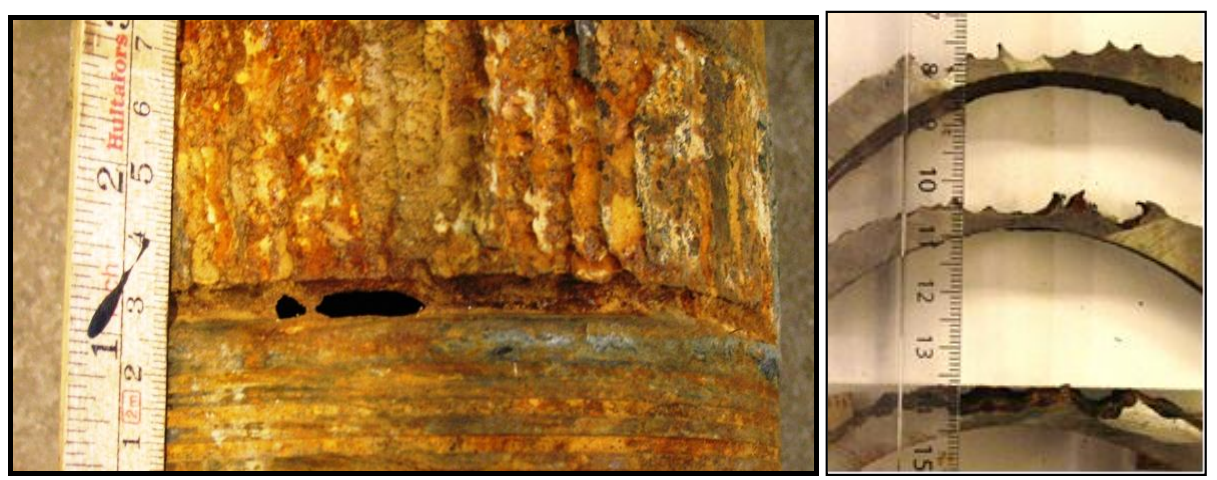
Şekil 5. 7” %3 Krom boruda şiddetli korozyon saldırısı.Şekil, çukurlu kimyasal enjeksiyon hattından üretim borusuna kireç önleyici püskürtüldükten sonraki korozyon saldırısını göstermektedir.
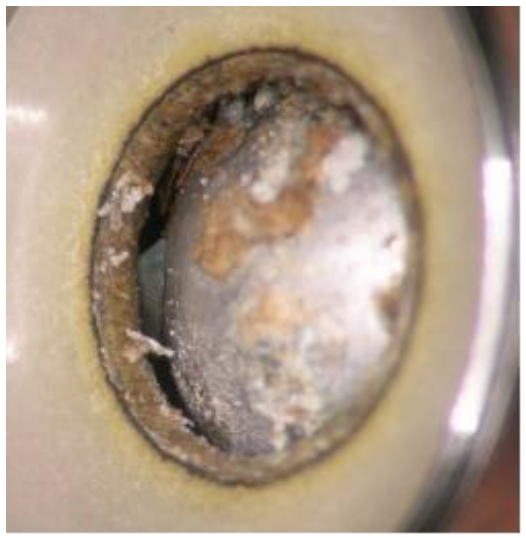
Şekil 6. Kimyasal enjeksiyon valfinde bulunan kalıntı.Bu durumdaki kalıntı, bazı beyazımsı döküntülere ek olarak muhtemelen kurulum sürecinden kaynaklanan metal talaşlarıydı.Beyaz kalıntıların incelenmesi, enjekte edilen kimyasalla benzer kimyaya sahip polimerler olduğunu kanıtladı.
Gönderim Zamanı: 27 Nisan 2022